The Role of PCBA in Modern Electronics Manufacturing
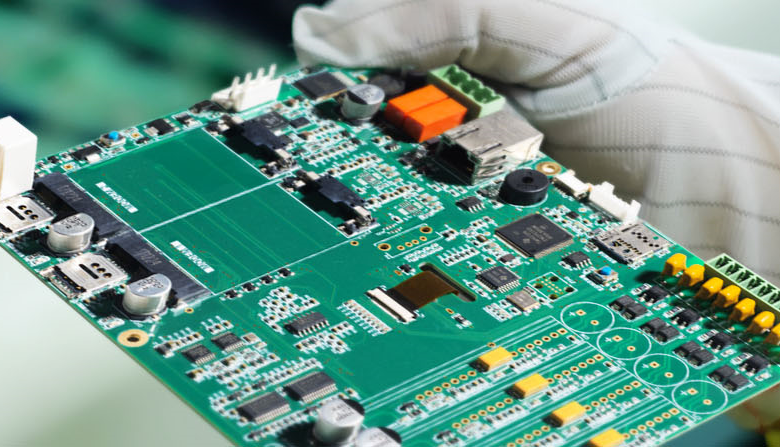
Printed Circuit Board Assembly (PCBA) is a fundamental process in modern electronics manufacturing. PCBA involves the assembly of electronic components onto a printed circuit board (PCB), transforming it into a functional and operational circuit. PCBA is critical in producing everything from consumer electronics, such as smartphones and laptops, to sophisticated industrial, medical, and aerospace equipment. The evolution of PCBA reflects broader trends in electronics, emphasizing miniaturization, efficiency, and precision in production.
Understanding PCBA
Before diving into the details of PCBA, it is important to understand the difference between a PCB and a PCBA. A PCB is simply the bare board—a substrate typically made of fiberglass, reinforced epoxy, or other laminate material—that has conductive paths etched into it. These paths create electrical connections between various components on the board. However, the PCB itself is not functional until it is populated with electronic components through the PCBA process.
PCBA is the step where various electronic components, such as resistors, capacitors, transistors, and integrated circuits (ICs), are soldered onto the PCB. This assembly process transforms the board into a working circuit that can power devices, manage data, or control machinery, depending on its intended purpose. Without PCBA, electronic devices would not be able to function.
The PCBA Process
The PCBA process generally consists of several key stages, each critical to ensuring a high-quality finished product. These steps can vary slightly depending on whether surface-mount technology (SMT) or through-hole technology (THT) is used, though SMT is the dominant method in modern manufacturing due to its advantages in speed, efficiency, and component density.
Solder Paste Application: The first step in the PCBA process involves applying solder paste to the PCB’s surface. This paste is a mixture of tiny solder balls and flux, which helps the solder flow and bond during the heating process. The paste is applied through a stencil that ensures it is placed only where components will be mounted. The precise placement of solder paste is critical for ensuring strong electrical connections between the PCB and the components.
Component Placement: Once the solder paste is applied, the electronic components are placed on the board. This step is typically done using automated machines, such as pick-and-place machines, which can rapidly and accurately place tiny components like resistors, diodes, and ICs onto the PCB. In high-volume manufacturing environments, these machines are essential for achieving the speed and precision necessary to meet production demands.
Soldering: After component placement, the board undergoes soldering to secure the components in place and create electrical connections. For SMT assemblies, reflow soldering is the most common method. In reflow soldering, the PCB is passed through a special oven where the solder paste melts and flows, forming solid electrical connections between the components and the board. For through-hole assemblies, wave soldering or manual soldering may be used, though these methods are more labor-intensive.
Inspection and Quality Control: Once soldering is complete, the board is inspected to ensure all components are properly connected and functioning as intended. Automated optical inspection (AOI) systems are commonly used to detect issues such as misaligned components, solder bridges, or missing parts. More advanced inspections, such as X-ray imaging, may be employed for complex boards to check hidden solder joints beneath components like ball grid arrays (BGAs).
Testing: After inspection, the assembled PCBA undergoes functional testing to verify that the circuit performs as expected. This may involve in-circuit testing (ICT), which checks the electrical connections, or functional testing (FCT), which simulates real-world operating conditions to ensure the board works correctly. Testing is crucial for identifying defects or issues before the product reaches the customer.
Cleaning and Final Assembly: In some cases, the PCBA must be cleaned to remove excess flux or contaminants left over from the soldering process. Once cleaned, the PCBA can be integrated into the final product or packaged for shipment.
The Importance of PCBA in Electronics
PCBA is at the heart of modern electronics. As devices become smaller, more complex, and more powerful, the need for reliable, high-quality PCBA processes becomes even more critical. The proliferation of miniaturized components, such as microprocessors and sensors, requires ever-greater precision in the assembly process. Surface-mount technology has allowed manufacturers to pack more components onto smaller boards, which has enabled the development of compact yet powerful devices, from smartphones and tablets to medical implants and wearable technology.
Moreover, the ability to automate much of the PCBA process through pick-and-place machines, reflow soldering, and AOI systems has drastically reduced production costs and increased efficiency. Automation also improves consistency, reducing the likelihood of defects and ensuring that each board functions as intended. This reliability is especially important in industries like aerospace, medical devices, and automotive electronics, where a single failure can have serious consequences.
Challenges and Innovations in PCBA
Despite its widespread use, PCBA faces several challenges, particularly as the demand for more compact, energy-efficient, and complex electronics continues to grow. One challenge is dealing with heat-sensitive components during the soldering process, which requires precise temperature control to avoid damage. Innovations such as lead-free solder and more sophisticated reflow ovens have helped address these issues, ensuring that boards meet stringent environmental and safety standards.
Another challenge is the ongoing push toward further miniaturization. As components shrink, placing them on PCBs requires increasingly fine tolerances and advanced machinery. In response, new techniques like 3D printing and additive manufacturing are emerging, which could revolutionize how PCBs and their assemblies are produced.
Conclusion
PCBA is a vital process in the electronics manufacturing industry, enabling the creation of the complex circuits that power modern devices. From its beginnings with through-hole technology to the adoption of surface-mount technology, PCBA has evolved to meet the demands of smaller, more powerful, and more reliable electronic products. As the technology continues to advance, the future of PCBA promises even greater precision, efficiency, and innovation in the world of electronics manufacturing.