Key Facts You Need to Know About Temperature Cycle Testing
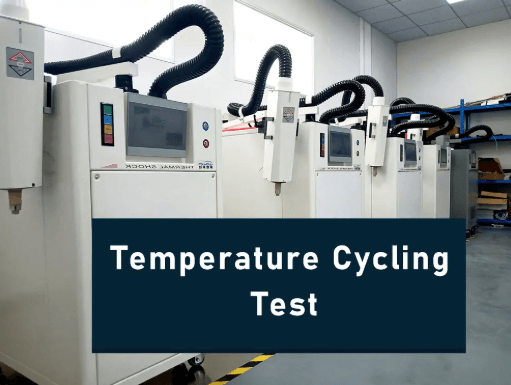
Temperature Cycle Testing is an important process that ensures the reliability of products under extreme conditions. It simulates real-world temperature fluctuations to assess how well products perform over time, preventing failures in critical industries like electronics, automotive, and aerospace. This testing is essential for ensuring durability and customer satisfaction making it a key element of product development. Understanding temperature cycle testing can help protect your investment and enhance the overall quality of your products.
What is Temperature Cycle Testing?
Temperature Cycle Testing is a method used to evaluate how materials and components react to extreme temperature changes. By exposing products to rapid heat and cold fluctuations, manufacturers can identify weaknesses that may not be apparent under stable conditions.
This testing simulates real-world scenarios, such as electronics enduring intense sunlight during the day and freezing temperatures at night. The product is placed in a controlled chamber, where temperatures are raised and lowered systematically over several cycles, simulating years of wear in a short period.
The test helps identify issues like thermal expansion, contraction, and material fatigue, preventing potential failures. It’s crucial for ensuring the reliability of products across industries, including consumer electronics and aerospace engineering.
How Does Temperature Cycle Testing Work?
Temperature cycle testing is a crucial process for evaluating the durability and reliability of products that may be exposed to fluctuating environmental conditions. Here’s a breakdown of how the test works:
- Product Placement: The product is placed inside a temperature-controlled chamber capable of rapidly altering its internal temperature.
- Temperature Variations: The product undergoes repeated cycles of high and low temperatures. These shifts simulate extreme environmental conditions that the product might face during its lifecycle, such as those experienced in outdoor or industrial settings.
- Stress Impact: The rapid temperature changes cause materials and components to expand and contract. This process generates stress on the product, helping to identify potential weaknesses that might not be visible under normal conditions.
- Monitoring: Sensors inside the chamber continuously track the product’s response to temperature changes. Key parameters such as expansion, contraction, and potential structural changes are recorded to identify issues.
- Failure Detection: Throughout the testing process, engineers observe for cracks, deformations, or other signs of failure, which could compromise the product’s performance or safety.
- Data Analysis: After completing the test engineers meticulously analyze the collected data to pinpoint flaws or weak spots. This helps in ensuring the product can withstand real-world conditions without failure.
The goal of temperature cycle testing is to simulate real-world stress to validate product design and ensure its longevity performance under extreme temperature fluctuations.
Benefits of Temperature Cycle Testing
Temperature cycle testing provides numerous benefits that significantly improve product development and performance:
- Early Detection of Failures: By simulating extreme temperature variations, temperature cycle testing helps identify potential product failures before market release. This proactive approach can prevent costly recalls and enhance customer satisfaction by ensuring higher-quality products.
- Material and Design Optimization: The test helps manufacturers understand how materials and components respond to thermal stress. This information allows for improved durability, better performance under real-world conditions, and more informed material choices during the design process.
- Compliance with Industry Standards: Many industries have stringent safety and reliability requirements. Temperature cycle testing ensures that products meet these regulatory standards, helping manufacturers stay compliant and avoid legal or safety issues.
- Resource and Time Savings: Identifying weaknesses early in the development process reduces the need for costly redesigns or testing. It also helps save time by preventing issues that could arise after mass production.
- Fosters Innovation: The data gained from testing enables engineers to refine designs and improve product features based on real insights rather than relying on assumptions. This iterative process encourages continuous innovation.
- Increased Competitiveness: By incorporating temperature cycle testing into their operations businesses can gain a competitive edge. The insights gleaned from this process aid in improving products and meeting elevated standards, potentially resulting in increased market acceptance and success.
Utilizing temperature cycle testing is crucial for enhancing product reliability, promoting efficiency, compliance, and innovation. This enables businesses to remain ahead in a competitive market.
Common Types of Tests in Temperature Cycle Testing
Temperature cycle testing employs several testing methodologies, each designed to assess the durability of a product under extreme temperature conditions. Here are some of the most common types:
- Thermal Shock Testing: This test exposes materials to rapid, extreme temperature changes, quickly shifting from high to low temperatures (or vice versa). The goal is to simulate real-world scenarios, such as moving electronics from an air-conditioned environment to a hot outdoor space. Thermal shock testing helps identify potential structural failures, cracks, or material weaknesses caused by sudden temperature transitions.
- Gradual Temperature Cycling: In this method, products are slowly cycled between high and low temperatures over extended periods (often hours or days). The gradual approach simulates stable environmental changes, like seasonal fluctuations, and evaluates long-term performance and durability. It helps assess how products cope with sustained thermal stress during typical use.
- Accelerated Life Testing: This test subjects products to harsher conditions than they would normally face in real-world environments to simulate an accelerated aging process. By pushing products beyond typical limits, manufacturers can predict lifespan and identify potential failures over the product’s entire lifecycle, even under extreme conditions.
Each of these methodologies helps engineers assess product durability under various temperature extremes, identifying weaknesses early in development and allowing for design refinements to ensure enhanced performance and reliability.
Challenges and Limitations of Temperature Cycle Testing
Temperature cycle testing is invaluable for assessing product durability, but it comes with several challenges and limitations:
- Replicating Real-World Conditions: The primary hurdle is accurately replicating real-world circumstances. Elements like humidity, atmospheric pressure, and temperature all play a role in how materials behave, making it challenging to control these factors during testing and therefore affecting the reliability of results.
- Material Unpredictability: Different materials may behave unpredictably under temperature fluctuations, with some exhibiting non-linear behavior or unexpected failure points. This can complicate assessments, especially when components don’t react as expected during cycling.
- Time and Cost: Comprehensive temperature cycle testing can be resource-intensive, requiring significant time and cost for setup, monitoring, and analysis. Extended cycles or accelerated life tests can strain resources, especially for companies with limited budgets or tight timelines.
- Data Interpretation: The intricate data from temperature cycle testing necessitates an expert analysis. Engineers must thoroughly scrutinize the results for any subtle indications of potential failure or material strain. Inaccurate interpretation could result in erroneous assumptions about the product’s dependability.
Despite its challenges, temperature cycle testing is crucial in product development. Overcoming its limitations requires careful planning, expertise, and sometimes additional testing methods to ensure reliable results.
Read also: Revolutionizing Web Design in Thanjavur: Aaradhana Technology Leads the Way
Integration of Temperature Cycle Testing in Product Development
Incorporating temperature cycle testing into product development is crucial for ensuring reliability. It allows engineers to simulate extreme conditions products may encounter during their lifecycle.
By integrating these tests early in the design phase, teams can identify potential weaknesses before they become urgent issues, enabling proactive adjustments rather than reactive fixes.
Temperature cycle testing also helps align products with industry standards and customer expectations, enhancing market trust. Collaboration between design and quality assurance teams is key to effective integration, fostering innovation while prioritizing durability.
This approach enhances product performance and boosts brand reputation by showcasing a commitment to quality testing strategies.